In the manufacturing industry, returns and replacements can be a common occurrence for many reasons — customer dissatisfaction, defective products, or incorrect orders, to name a few. To manage these processes systematically in a manufacturing company, an RMA (Return Merchandise Authorization) is required. With the help of Dynamics 365 Supply Chain Management (D365 DSCM), companies can handle the RMA process seamlessly, ensuring customer satisfaction and a smooth back-end operation. This post will provide a high-level overview of the RMA process in Dynamics 365 Supply Chain Management, along with some real-world scenarios of RMA handling in a manufacturing company and highlight the benefits of an efficient RMA process.
What Is an RMA?
An RMA is a process by which a manufacturing company manages, and tracks returns or replacements of its products. It involves creating a record of the returned items specifying the reason for the return, and the type of remedy required — refund, replacement, or repair. The RMA process helps companies track the status of returned products and enables them to refund or replace the items as quickly as possible, reducing the impact on customer experience.
How to Handle RMA in Dynamics 365 Supply Chain Management
D365 SCM includes a feature in the Inventory and Warehouse Management module that simplifies the RMA process for manufacturing companies. This feature facilitates the creation of RMAs by specifying the product code, quantity, reason code for the return, and the remedy type on a return order. After creating an RMA, the system generates a unique RMA number and assigns it to the record, simplifying tracking and management. Integration with other modules, such as Inventory, Production, and Sales can further streamline the RMA process to ensure transparency and accuracy.
Example of RMA Handling in a Manufacturing Company
Let’s consider a real-world scenario of RMA handling in a manufacturing company.
A customer purchased a TV system and accessories that were delivered with a defective speaker cable. The customer contacts customer service, and they raise an RMA for the product. The manufacturing company receives the request, inspects the cables, and verifies the issue. The RMA record is updated with the current status, and a replacement is initiated. Once the replacement is ready, it is shipped to the customer, and the RMA is marked as closed.
Steps to Creating an RMA in Dynamics 365 Supply Chain Management
- Navigate to Accounts receivable > Return orders
- Additional, you can use the Sales Return workspace
- Select New to create a new return order
- Specify the Sales Order, returned item(s), reason code for return, and remedy type information.
- Click Ok to generate an RMA number for the record.
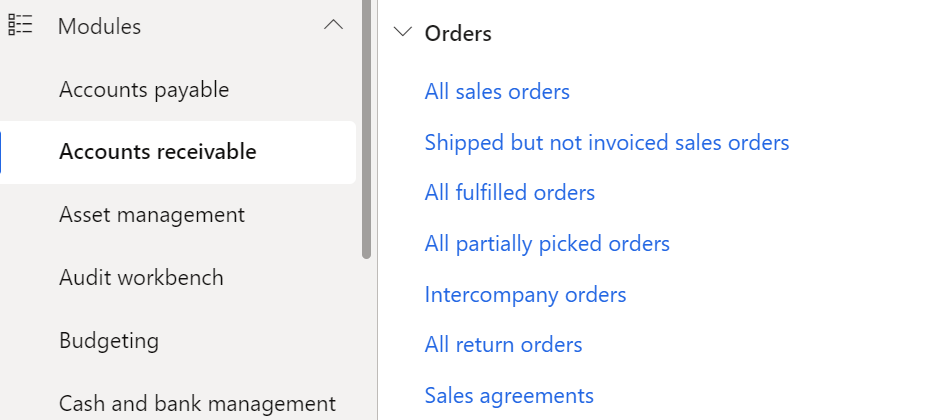
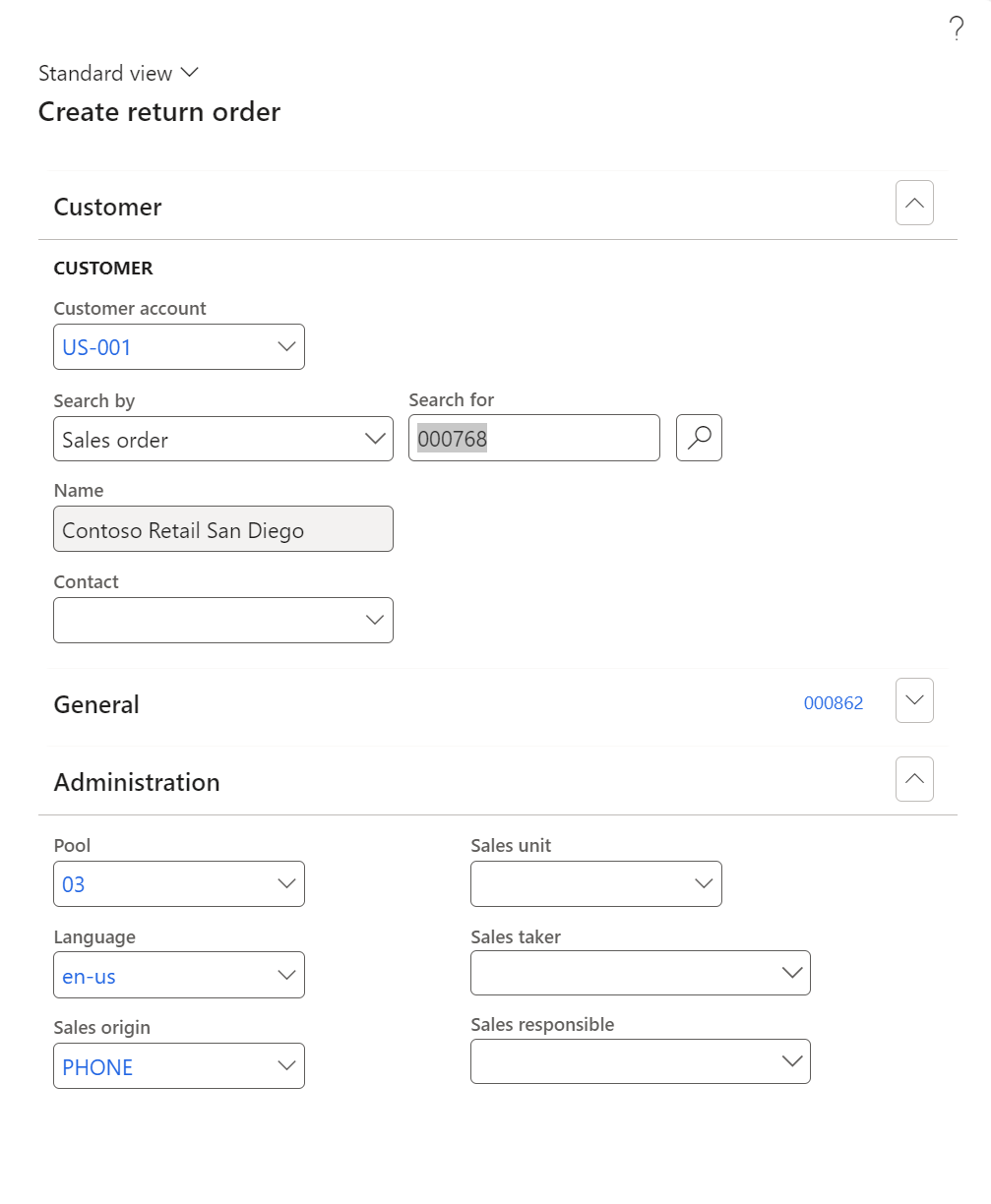
Updating the RMA After Inspection and Issue Verification
- Locating the Existing RMA: Navigate to Accounts Receivable and select Return Orders
- Locate and choose the specific RMA using the RMA number or other search criteria
- Access the RMA Record: Once located, access the record to view its details
- Update the RMA Line for Inspection: Navigate to the line item representing the cables
- Adjust the status: Adjust the status or (if applicable) custom field to indicate the items have been inspected

Once the returned item has been inspected and the issue verified, updating the RMA status in D365 SCM is crucial for maintaining accurate records and communicating the next steps to the customer. Here are the steps to update an RMA after inspection:
- Entering Inspection Details
- Include notes or comments in the RMA line or in a designated field to document the outcome of the inspection
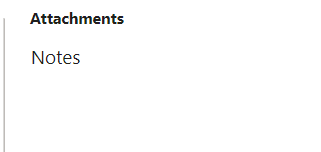
- Changing the Status of the RMA Line
- If the inspection results in a specific action such as repair, return, replacement, or credit, ensure that the RMA line status is updated accordingly
- Once all necessary updates and entries have been completed, save the changes
- Verify that all information is accurately recorded and reflects the current status of the return process
- Communicating with the Customer
- If your process involves informing the customer about the inspection results, utilize appropriate channels
Benefits of an Efficient RMA Process
An efficient RMA process helps manufacturing companies enhance customer satisfaction, reduces waste of resources, increases productivity, and enhances the overall customer experience. By minimizing the impact of returns and replacements, companies can also increase brand credibility and loyalty. An effective RMA system can also help companies identify improvement areas in their product development, production, and supply chain processes, enabling them to take corrective actions, ultimately improving the quality of their products.
In, managing returns and replacements can be a complex process for any manufacturing company. The RMA module in D365 Supply Chain Management simplifies the process, making it easier to manage, track, and execute returns and replacements. By leveraging technology, manufacturing companies can enhance their customer satisfaction, optimize resource utilization, and improve the efficiency of their operations. Effective RMA processes play a crucial role in the success of a manufacturing company, and an efficient RMA system is a necessary component of any modern manufacturing operation.
The post Understanding RMA in Dynamics 365 Supply Chain Management: Returns and Replacements appeared first on Dynamics Communities.