The physical inventory order is a better way to do stock counts in Dynamics 365 Business Central. It breaks down a large task into smaller, more manageable pieces.
It allows users to subdivide the count of inventories by warehouse and to create more than one registration of the inventories by single order of inventory (segmentation of the inventories); in practice, everyone counts their own items in their own warehouse to then gather all the counts.
In the case of serial batch use it is possible to divide the lines to be able to count additional batches and serial numbers; in practice, it is an open and comfortable system to use.
Scope of the Feature
You can take a physical inventory of your items by using physical inventory order and physical inventory recording documents. The Physical Inventory Order page is used to organize the complete inventory counting project, for example one per location. The Physical Inventory Recording page is used to communicate and capture the actual counting of items. You can create multiple recordings for one order, for example to distribute groups of items to different employees.
The Physical Inventory Recording report can be printed from each recording and contains empty quantity fields for entering the counted inventory. When a user is done counting, and the quantities are entered on the Physical Inventory Recoding page, you choose the Finish action. This transfers the quantities to the related lines on the Physical Inventory Order page. Functionality ensures that no item count can be recorded twice.
Counting inventory by using documents consists of the following overall steps:
- Create a physical inventory order with expected item quantities prefilled.
- Generate one or more physical inventory recordings from the order.
- Enter the counted item quantities on the recordings, as captured on printouts, for example, and set it to Finished.
- Complete and post the physical inventory order.
As compared to older methods like the physical inventory journal, the order:
- Provides a more flexible method for inventory count
- Alleviates some of the challenges or need for custom modifications around inventory counting when you use lot number or serial number tracking
- Simplifies distributing inventory count to several warehouse staff
- Integrates very well with scanning devices
- Provides a solution to your warehouse count when directed pick and put-away is not enabled
How to Use a Physical Inventory Order
- Decide on a plan. Determine how you would like to perform the count:
- by location,
- by item, or
- by bin
- Search for “Physical Inventory Orders” within Business Central.
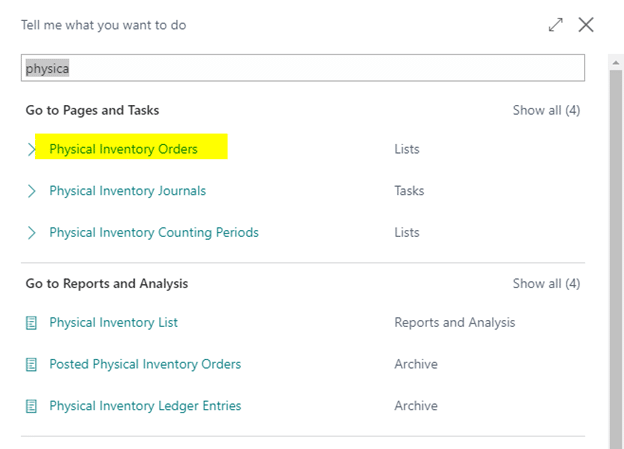
3. Create a new physical inventory order.
4. Provide a description for your stock count and specify the location that you wish to count. You can also assign yourself or another member of the team to oversee the count.
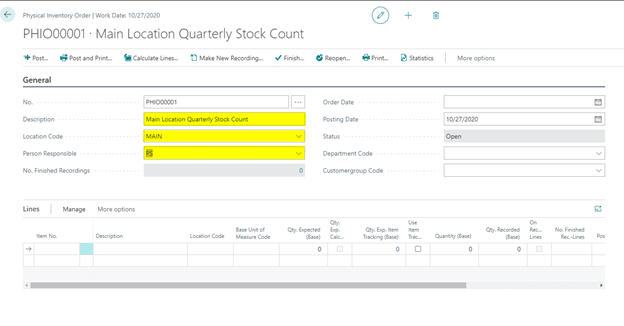
5. Use the “Calculate Lines” function to obtain the current system count. Note: You can do this by Counting Period or Bins. By filtering to the location only, the system will provide you with the expected inventory quantity for each item that you had transacted before.
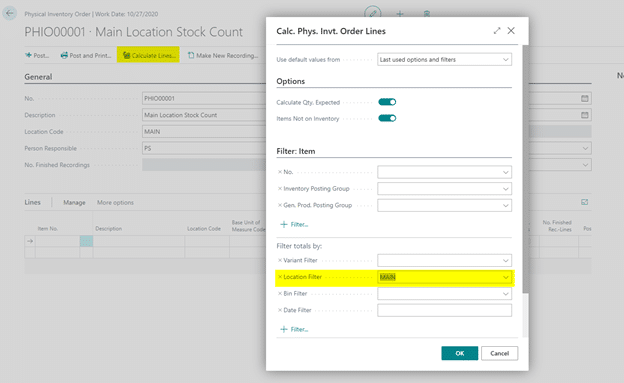
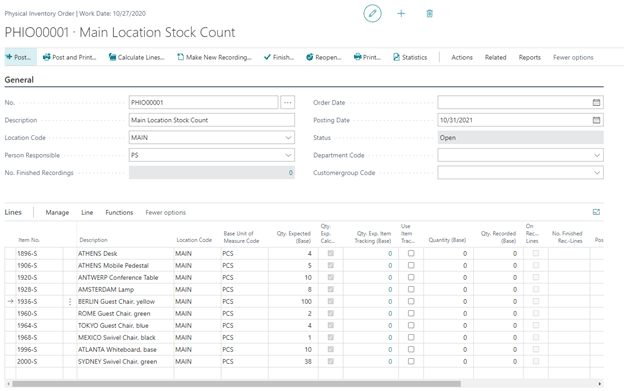
However, you might want to prepare the count sheet a couple days in advance. If so, you can always click on “Calc. Qty Expected”, if there is a date difference between when you started the worksheet and when the user is actually going to perform the count.
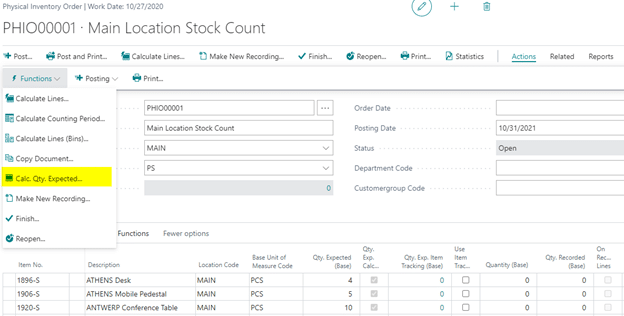
6. Use “Make New Recording” to create a subset of your inventory count.
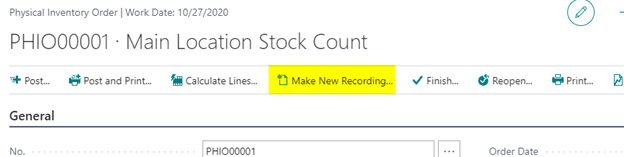
You can create your physical record by bin number, item category, or product type so you can
- Distribute the tasks to multiple warehouse staff to count by aisle
- Distribute the task by item category or product posting group
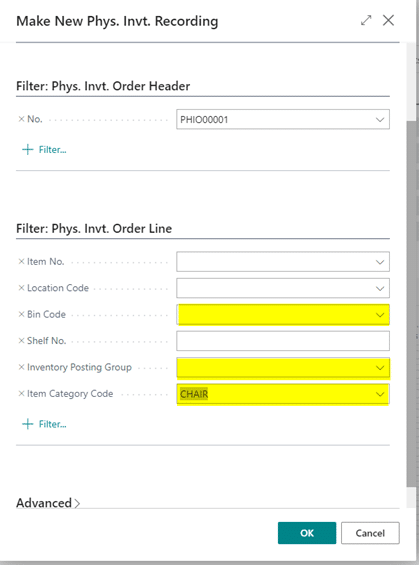
In this example, let’s say we’ll create 2 recordings out of the physical inventory order. One recording is assigned to one warehouse user, Annette Hill, who would count only CHAIR Items.
Then another user, John Richards, would count the remaining items.
7. Go to Phys. Inventory Recording list.
Open the physical inventory recording. Assign Annette (AH) to process Recording 1 and John (JR) to process Recording 2.
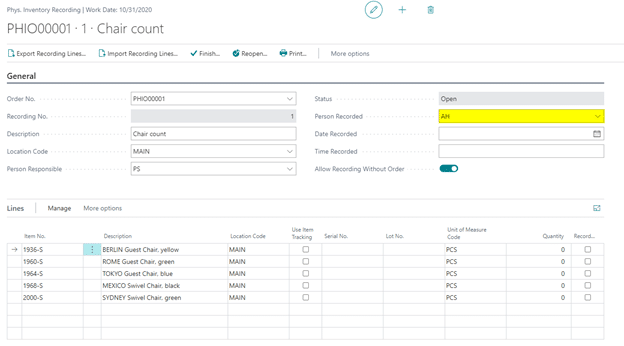
8. During the recording, if your organization uses lot number or serial number tracking, you can fill out the lot number on the line level. If you have found an item that did not show up on the original list, you can also add the item ad hoc.
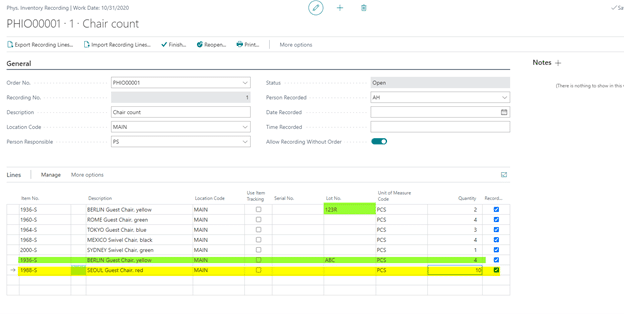
Click on Finish when you are done with the recording.
9. While you are on the physical inventory order page, you can monitor the number of finished recordings, the quantity expected, and quantity recorded. Note: When the Qty. Exp. Calc. box is not checked for a line, that indicates the line does not exist in the original plan. This means you may not have it on hand according to the system or you may not have ever transacted with it. If so, please select Action > Function > Calculate Expected Quantity to update the line.
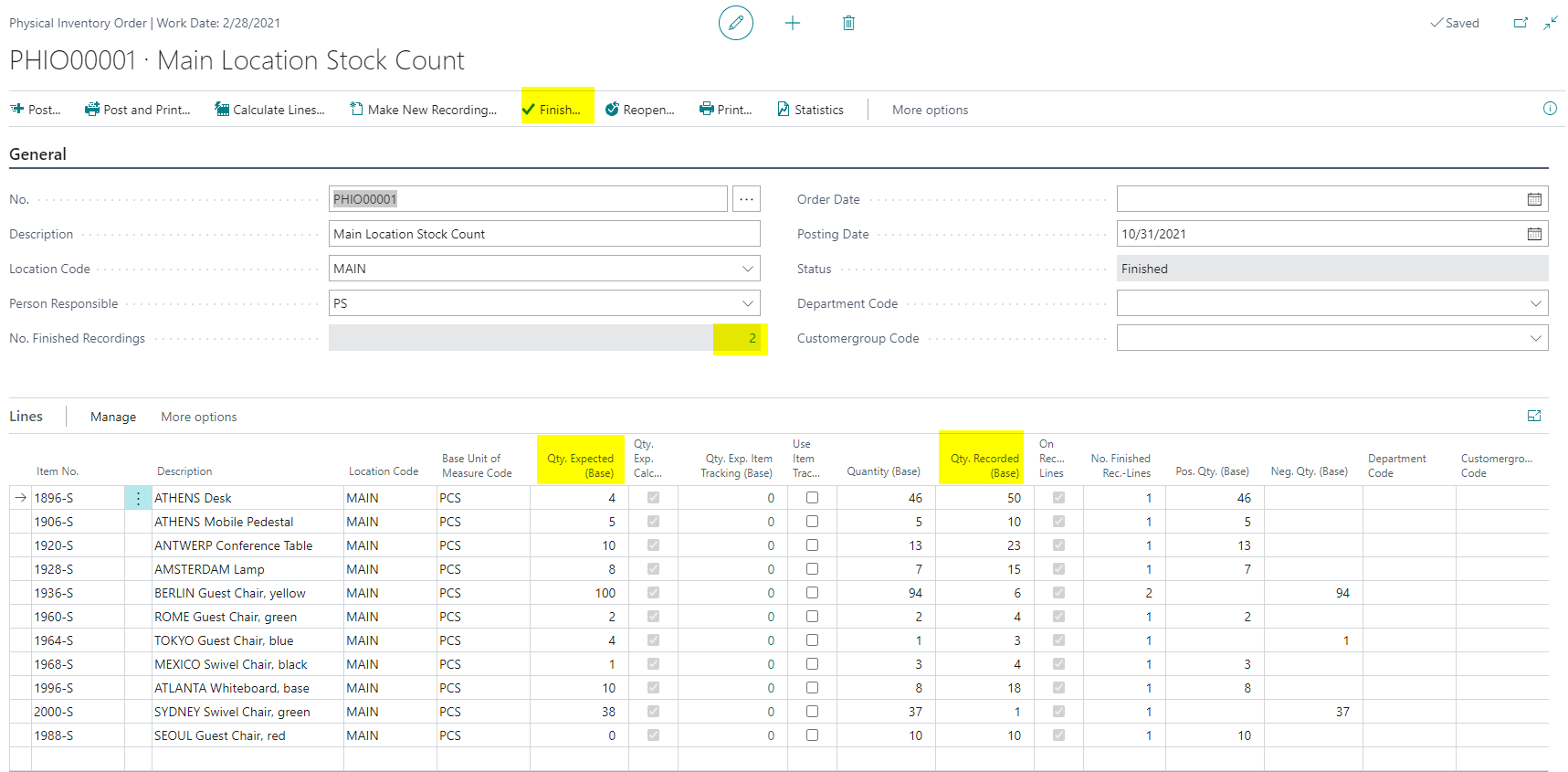
10. Click on Finish to finalize the count when you and your team are done. The system will then calculate positive and negative adjustment for each line.
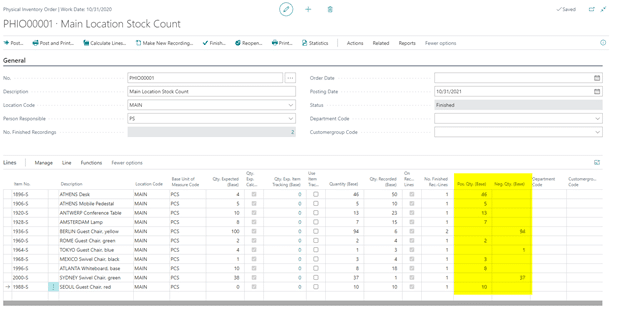
11. Print the Invt. Order Diff. List to get a report view.
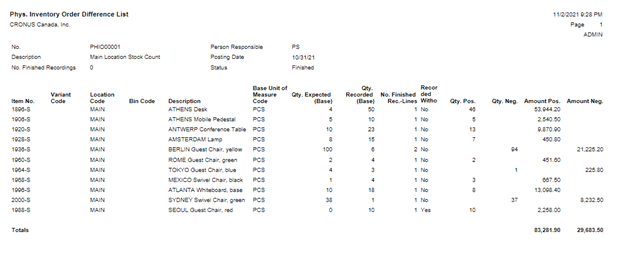
FAQs
What if purchase and sales transactions happen between when I create the order and start the count?
No problem. Use the Calc. Qty. Expected function to get the latest calculated quantity.
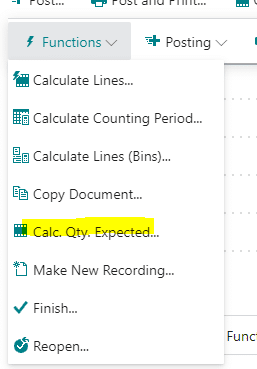
What if I have found an item that does not exist on the list?
Just go ahead and add the item onto the recording. Select Calculate Qty. Expected on the physical inventory order when you are nearly completed.
What if I have multiple lot numbers to count for the same item?
Simply add a new line to your recording.
The post How to Use Physical Inventory Orders in Dynamics 365 Business Central appeared first on Dynamics Communities.