Routing Link Codes are used in Dynamics 365 Business Central to link specific components of a production bill of material to operations within a production routing. This ensures that components are available when needed, reducing inventory costs and increasing production efficiency.
The link between the component and the routing operation ensures that component inventory is only required when the operation is scheduled to start, rather than at the beginning of the production order. This is useful in complex production processes where components are needed at different stages.
The benefits of using routing link codes include:
- Efficient Inventory Management – Reduction of inventory on hand, lowering inventory holding costs.
- Improved Production Scheduling – Components can be scheduled based on when they are needed.
- Flexibility – If there are changes in the production process or schedule, it is easier to adjust component delivery schedules based on when components will be needed.
- Traceability – Provides clear traceability of component through the production process, making it easier to manage and troubleshoot production issues.
How to Set Up Routing Link Codes
Define Routing Link Codes
- Search “Routing Links.”
- Enter new Codes and enter a description for each:
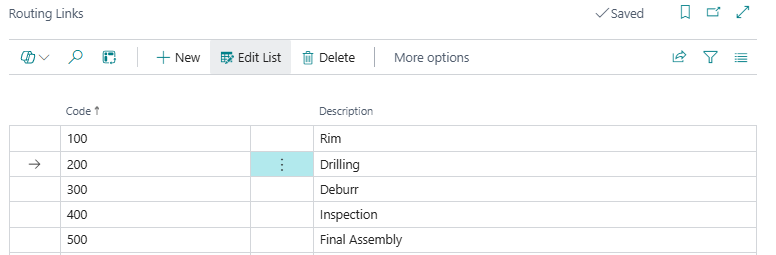
Update Routing
- Enter a valid routing link code for each operation in your production routing as needed. These codes will later be used to link production components to the routing operations.
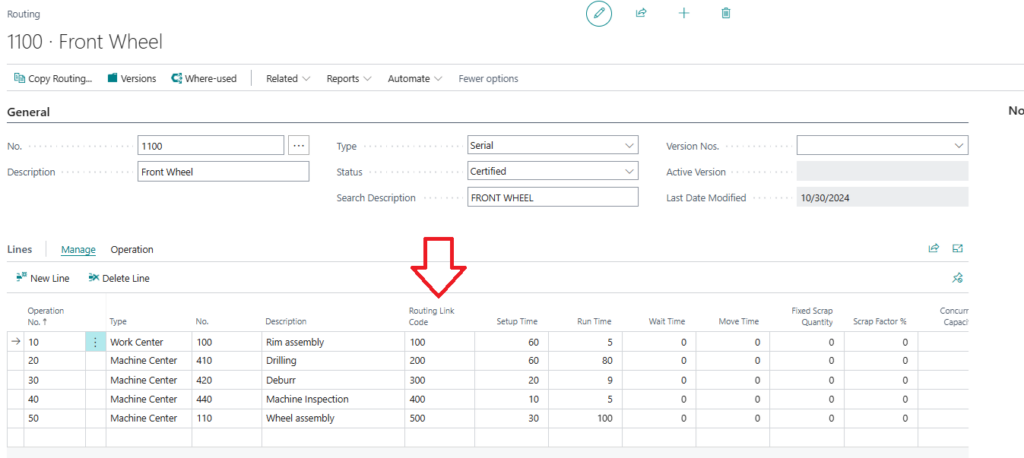
Update Production BOM
- Enter a valid routing code for each component as needed. This will complete the link of components to specific routing operations.
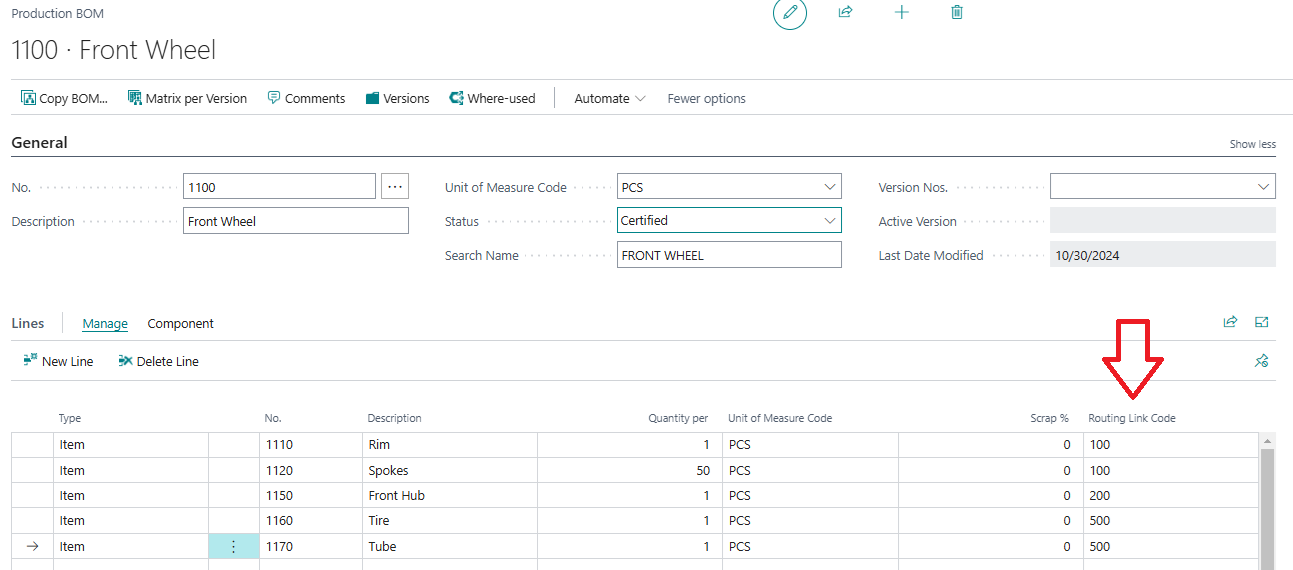
2. Review the routing link code setups above and ensure that the production routing and BOM both have a certified status.
3. Now when creating a production order, you can review component due dates to see the effect of using routing link codes since BC will automatically link components to operations.
Example
Production order component due dates when NOT using routing link codes – all components have the same due date:

Production order component due dates when using routing link codes – component due dates vary based on when each component is needed:

In this example, all my components are backflushed, therefore, when I go to the Production Journal, I will only see output lines and there is one output line for each routing operation. (The same would be true if using the Output Journal)
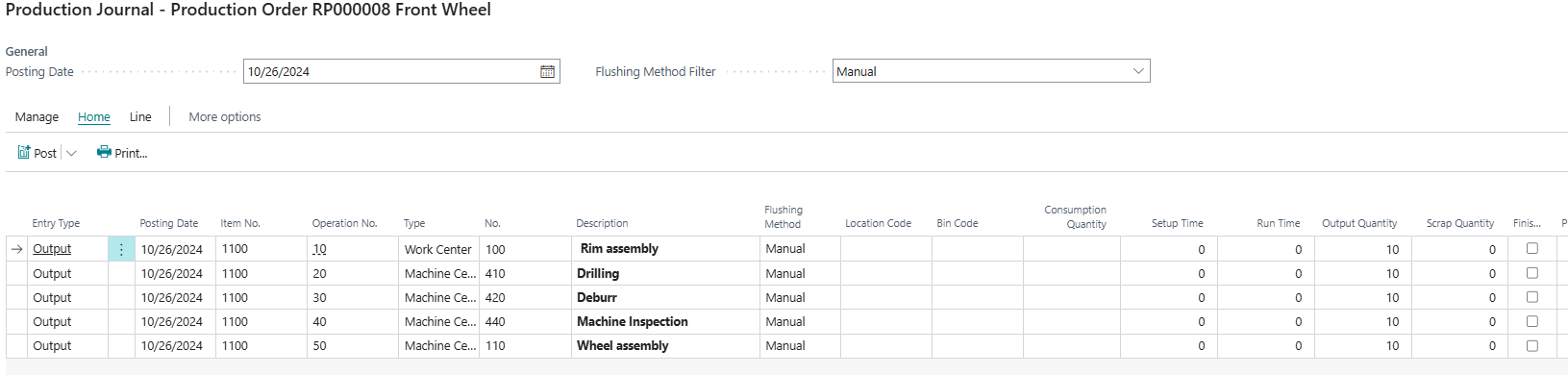
I can post output for each operation individually and consumption will occur only for components linked to the operation posted.
When I post output only against operation 10, only components 1110 and 1120 are consumed since they are the only components linked to operation 10.
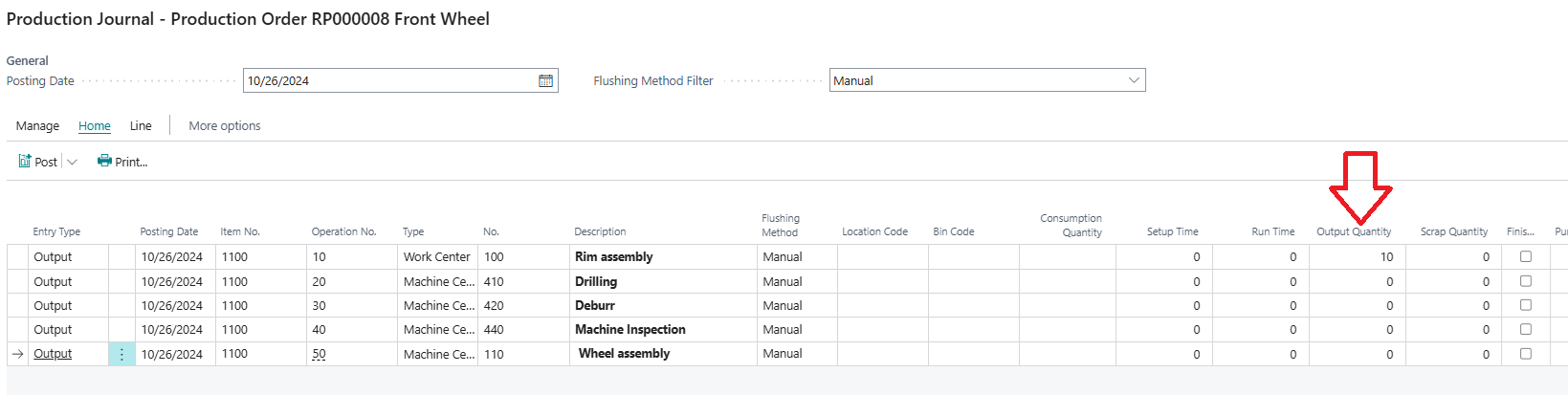
Here you can see that only the components linked to operation 10 have been consumed.

To learn more or have any questions answered, please reach out to me or post your questions and comments on the Dynamics Communities discussion board.
The post Understanding Routing Link Codes in Business Central appeared first on Dynamics Communities.