In the manufacturing industry, quality inspection is a crucial process that ensures products meet certain standards and specifications. Quality inspection involves checking for defects, identifying areas of improvement, and ensuring that products are safe and functional before they are delivered to customers.
With the advancement in technology, manual quality inspection processes have become inefficient and time-consuming. This has led many companies to adopt automated quality inspection systems to improve the accuracy and speed of their inspections. One system is Dynamics 365 Finance & Operations (D365FO).
D365FO provides powerful tools to manage various business processes, including quality control. In this post, we will explore how D365FO can help organizations streamline
Setting Up Quality Management
Before starting inspections, establish a quality management framework in D365FO that includes:
- Defining Quality Associations: Automatically trigger quality orders based on specific events or criteria.
- Creating Test Groups: Assign tests with acceptable quality levels (AQLs).
- Setting Up Sampling Plans: Determine the quantities to inspect.
- Configuring Quarantine Zones: Designate areas for storing non-conforming items.
The Quality Inspection Process
1. Initiating Quality Orders
Quality orders in D365FO can be created either automatically or manually:
- Automatic Creation: Triggered by predefined quality associations, such as receiving a purchase order from a particular vendor.
- Manual Creation: Users can generate quality orders as needed, including for ad-hoc inspections.

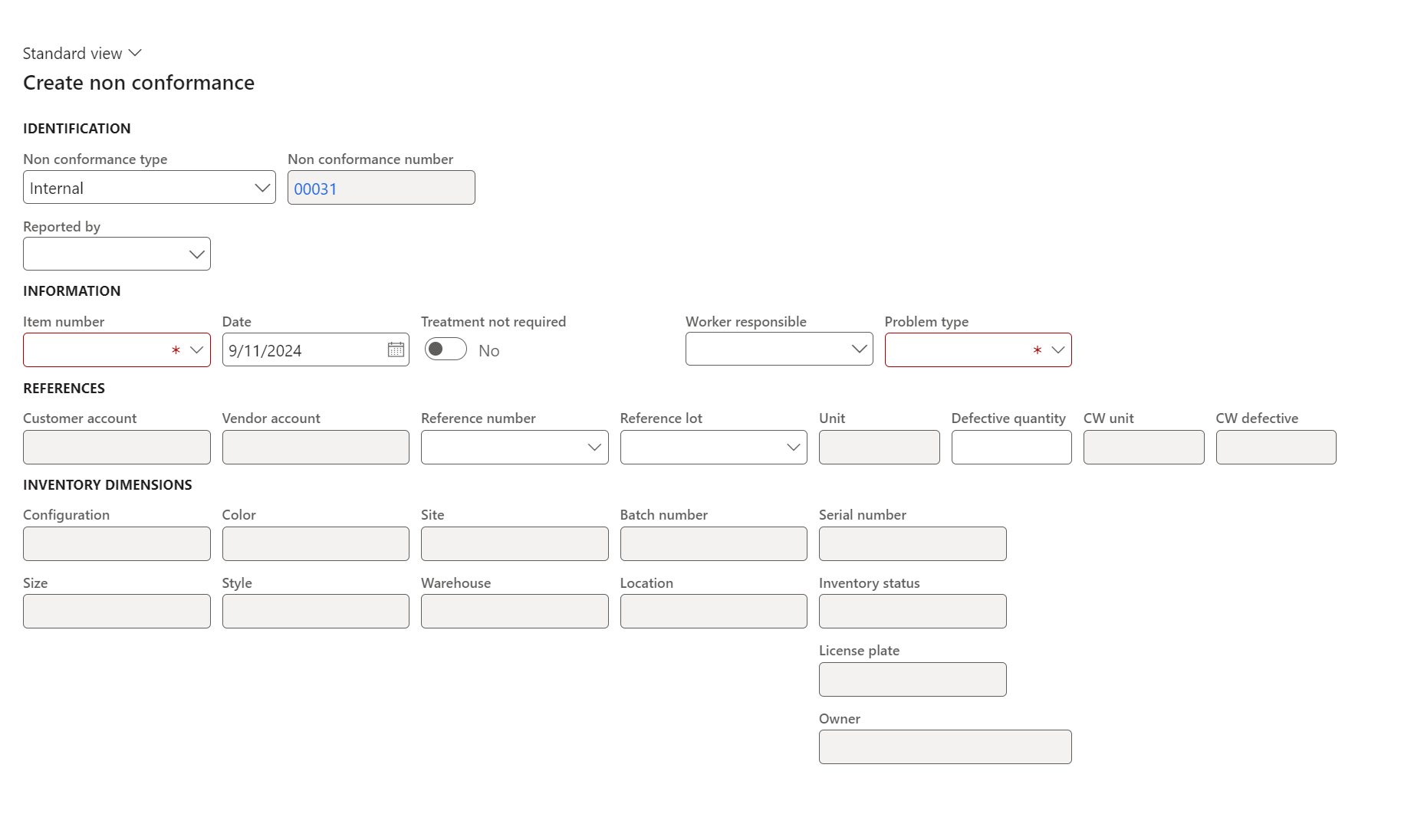
2. Performing Inspections
Inspectors can record test results directly within the system:
- Enter Results: Document quantitative or qualitative test results.
- Compare Against AQLs: Ensure results meet predefined standards.
- Attach Documents: Add supporting documents or images to the quality order.
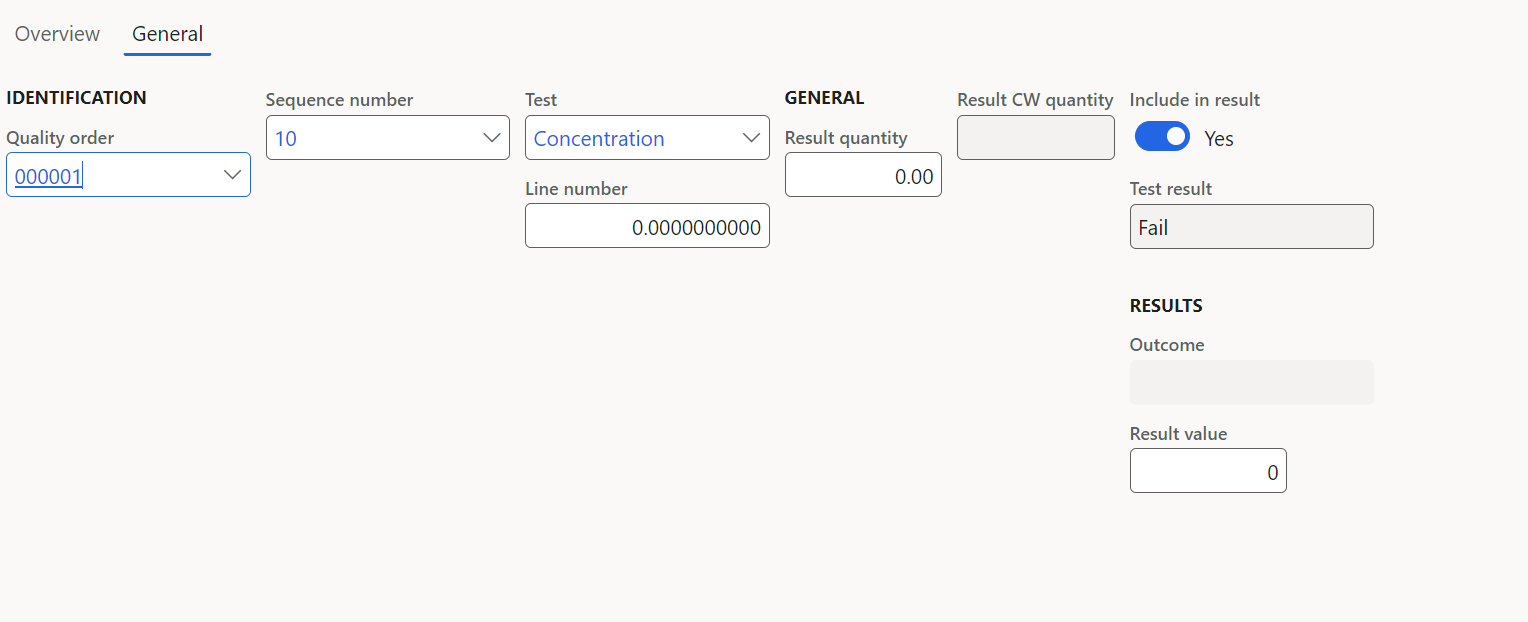
3. Evaluating Results
D365FO automatically evaluates test results against established criteria:
- Pass/Fail Determination: Based on AQLs.
- Quality Rating Calculation: Provides an overall quality rating.
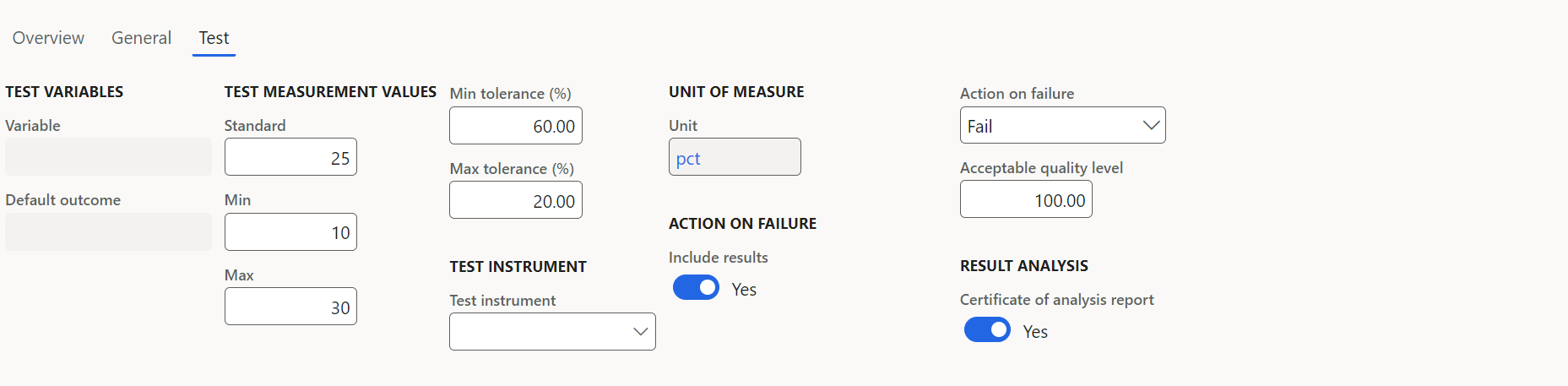
4. Issuing Quality Certificates
For items that pass inspection, D365FO enables:
- Generation of Quality Certificates.
- Inventory Status Update: Automatically updates the inventory status to make items available for use or sale.
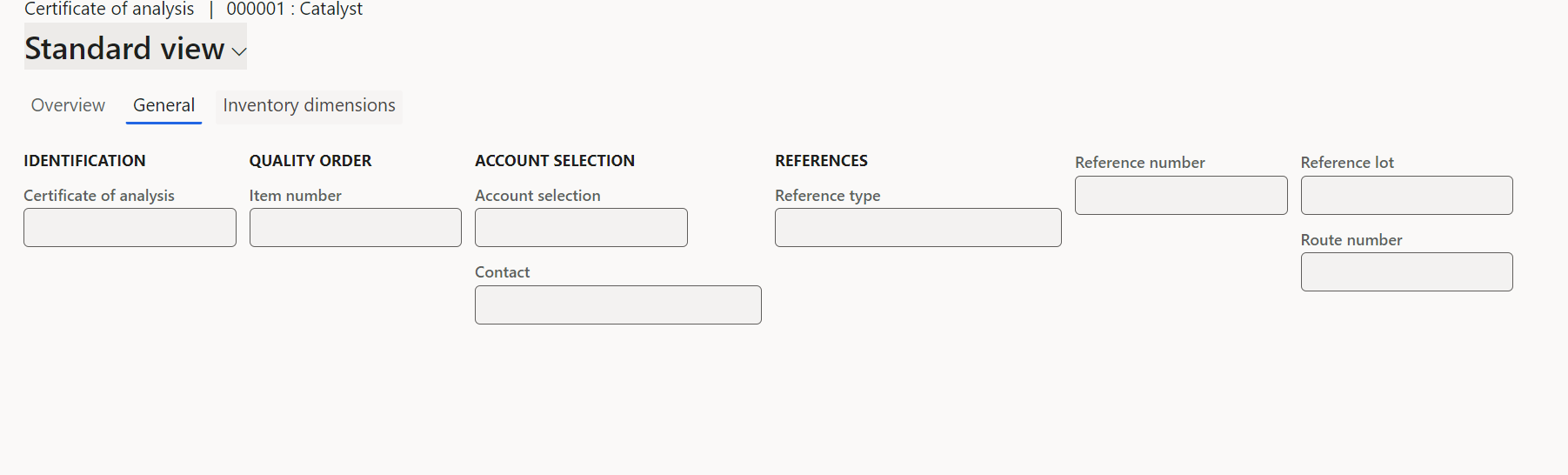
Handling Non-Conformances
When quality issues arise, D365FO offers tools to manage non-conformances effectively:
- Creating Non-Conformances: Generate records directly from quality orders or independently.
- Approval Process:
- Initial status is set to “New”.
- Quality managers approve or reject the non-conformance.
- Documenting Issues:
- Record problem type and description.
- List affected items or processes.
- Conduct root cause analysis.
- Assigning Responsibility: Allocate tasks to workers responsible for addressing the non-conformance.
- Quarantine Management: Move non-conforming items to designated quarantine zones.
Corrections and Follow-up
For approved non-conformances, D365FO supports the correction process:
- Planning Corrections:
- Define actions required.
- Assign personnel.
- Set target completion dates.
- Tracking Progress: Monitor the status and updates of corrections.
- Documenting Corrections: Record details of corrective actions taken.
- Closure: Close non-conformances once corrections are completed.
Reporting and Analysis
D365FO provides robust reporting capabilities for quality management:
- Non-Conformance Reports: Generate detailed reports on quality issues, including root causes and corrective actions.
- Correction Reports: Document specific measures taken for non-conformances.
- Quality Analytics: Utilize Power BI integration for in-depth analysis of quality trends and performance metrics.
Continuous Improvement
Data collected through the quality inspection process in D365FO supports continuous improvement initiatives:
- Identify Recurring Quality Issues.
- Analyze Supplier Performance.
- Optimize Inspection Processes based on historical data.
By leveraging D365FO’s quality management capabilities, organizations can ensure consistent product quality, reduce waste, and improve customer satisfaction. The system’s integrated approach to quality inspection, non-conformance handling, and corrective actions provides a comprehensive solution for maintaining high-quality standards throughout the supply chain.
The post Exploring Quality Inspection with Dynamics 365 Finance & Operations appeared first on Dynamics Communities.